Definition
An alloy is defined as “homogeneous solid solution of two or more different element one of which at least is essentially a metal”. Alloy containing Hg as a constituent element are called amalgams.
Properties of alloys
· Alloy are harder less malleable and possess lower melting point than their component metals
· Alloys possess low electrical conductivity
· Alloys resist corrosion and the action of acids
Importance or need of making alloys
1. To increase the hardness of the metal Example
Gold and silver are soft metal they are alloyed with copper to make them hard
2. To lower the melting points of the metal Example
Wood metal (an alloy of lead, bismuth, tin and cadmium) melts at 60.5⁰c which is far below the melting points of any of these constituent metals
3. To resist the corrosion of the metal
Example
Pure iron rested but when it is alloyed with carbon chromium (stainless steel) which resists corrosion
4. To modify chemical activity of the metal
Example
Sodium amalgam is less active than sodium but aluminium amalgam is more active than aluminium
5. To modify the colour of the metal Example
Brass an alloy of copper (red) and size (silver-white) is white colour.
6. To get good casting of metal Example
An alloy of lead with 5% tin and 2% antimony is used fro casting printing type due toits good casting property
Functions (or) effects of alloying elements
Addition of small amount of certain metals such as Ni, Cr, Mo, Mn, Si, v and Al impart special properties like hardness, tensile strength, resistance to corrosion and coefficient of expansion on steel. Such products are known as special steel or alloy steels Some important alloying element and their functions are given in table
CLASSIFICATION (OR) TYPES OF ALLOYS
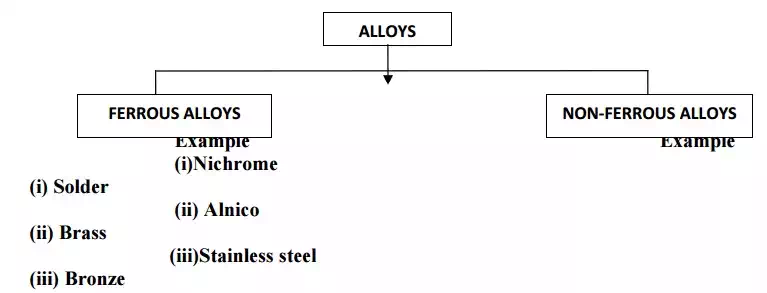
FERROUS ALLOYS OR ALLOY STEELS
Ferrous alloys are the type of steels in which the elements like Al,B,Cr,Co,Cu,Mn are present in sufficient quantities, in addition to carbon & iron.
PROPERTIES
1. High yield point & strength
2. Sufficient formability,ductility & weldability
3. Corrosion & abrasion resistant
4. Less distortion & cracking
5. High temperature strength
IMPORTANT FERROUS ALLOYS (i)NICHROME
Nichrome is an alloy of nickel & chromium
COMPOSITION
Nickel – 60%
Chromium – 12%
Iron – 26%
Manganese – 2%
PROPERTIES
1. Good resistance to oxidation & heat
2. High melting point & electrical resistance
3. Withstand heat up to 1000-1100⁰C
USES
1. Used for making resistance coils,heting elements in stoves & electric irons
2. Used in making parts of boilers,steam lines stills,gas turbines,aero engine valves,retorts,annealing boxes.
(ii)ALNICO
Alnico is an alloy of aluminium-nickel-cobalt .
COMPOSITION
Aluminium – 8-12%
Nickel – 14-28%
Cobalt – 5-35%
PROPERTIES
1. Excellent magnetic properties & high melting point
2. Magnetized to produce strong magnetic fields as high as 1500 gauss
TYPES OF ALNICO ALLOYS
Alnico alloys are of two types
1. ISOTROPIC ALNICO
It is effectively magnetized in any direction
2.ANISOTROPIC ALNICO
It possess preffered direction of magnetization.
Anisotropic alnico possesses greater magnetic capacity in their preffered orientation than isotropic alnico.
USES
1. Used as permanent magnets in motors,generators,radio speakers microphones,telephone receivers & galvanometers.
(iii)STAINLESS STEELS (or)CORROSIOPN RESISTANT STEELS
· These are alloy steels containing chromium together with other elements such as nickel,molybdenum,etc.
· Chromium-16% or more
· Carbon-0.3-1.5%
PROPERTIES
1. Resist corrosion by atmospheric gases & also by other chemicals.
2. Protection against corrosion is due to the formation of dense, non-porous,tough film of chromium oxide at the metal surface. If the film cracks, it gets automatically healed up by atmospheric oxygen
TYPES OF STAINLESS STEEL
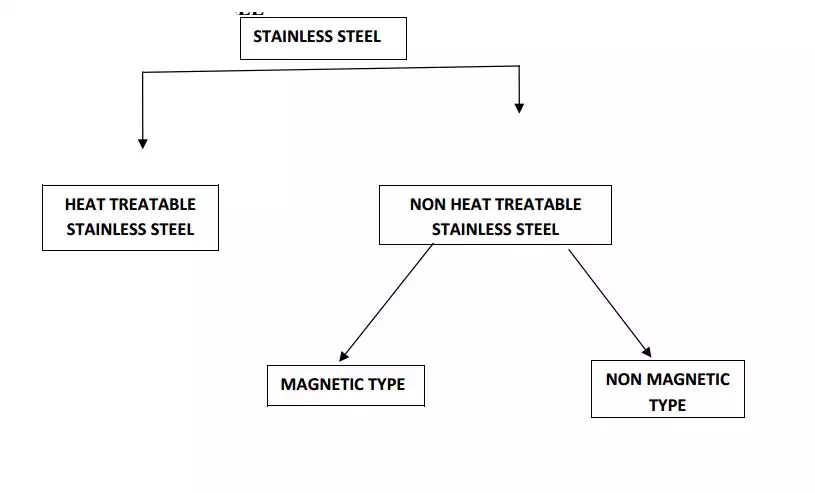
1. HEAT TREATABLE STAINLESS STEEL
COMPOSITION Carbon-1.2%
Chromium-less than 12-16%
PROPERTIES
Magnetic,tough & can be worked in cold condition
USES
1. Can be used up to 800⁰C
2. Good resistant towards weather & water
3. In making surgical instruments,scissors,blades,etc.
2.HEAT TREATABLE STAINLESS STEEL
PROPERTIES
· Possess less strength at high temperature
· Resistant to corrosion
TYPES OF NON HEAT TREATABLE STAINLESS STEEL
(a)MAGNETIC TYPE
COMPOSITION
Chromium-12-22%
Carbon-0.35%
PROPERTIES
1. Can be forged,rolled & machined
2. Resist corrosion
USES
Used in making chemical equipments& automobile parts.
(b)NON MAGNETIC TYPE
COMPOSITION
Chromium-18-26%
Nickel-8-21% Carbon-0.15%
Total % of Cr & Ni is more than 23%. EXAMPLE:18/8 STAINLESS STEEL COMPOSITION: Chromium-18%
Nickel-8%
PROPERTIES
1. Resistance to corrosion.
2. Corrosion resistance is increased by adding molybdenum
USES
In making household utensils,sinks,dental & surgical instruments.
NON FERROUS ALLOYS
· Do not contain iron as one of the main constituent.
· Main constituents are copper,aluminium,lead,tin,etc.
PROPERTIES
1. Softness & good formability
2. Attractive (or) very good colours
3. Good electrical & magnetic properties
4. Low density & coefficient of friction
5. Corrosion resistance
IMPORTANT NON FERROUS ALLOYS 1. COPPER ALLOYS (BRASS)
Brass contains mainly copper & zinc
PROPERTIES
· Greater strength, durability & machinability
· Lower melting points than Cu & Zn
· Good corrosion resistance & water resistance property
2.BRONZE(COPPER ALLOY)
Bronze contains copper & tin
PROPERTIES
· Lower melting point
· Better heat & electrical conducting property
· Non-oxidizing,corrosion resistance & water resistance property.
3.SOLDERS
Solders are low- melting alloys of tin & lead
PROPERTIES
Solder is melted to join metallic surfaces ,especially in the fields of electronic &
plumbing
USES
1. Used in electrical industry
2. Alloy with 50% tin is general-purpose solder
3. For sealing automotive radiator cores.
4. As fuses for fire-extinguishing equipments,boiler plugs,etc.
Heat treatment of alloys (steel)
Heat treatment is defined as” the process of heating and cooling of solid steel article under carefully controlled condition”. During heat treatment certain physical properties are altered without altering its chemical composition
Objectives (or) purpose of heat treatment
Heat treatment causes
i. Improvement in magnetic and electrical properties
ii. Refinement of grain structure
iii. Removal of the imprisoned trapped gases
iv. Removal of internal stress
v. Improves fatique and corrosion resistance
Types of heat treatment of alloys (steel) 1. Annealing
Annealing means softening. This is done by heating the metal to high temperature followed by slow cooling in a furnace.
Purpose of annealing
i. It increases the machinability
ii. It also removes the imprisoned gases
Types of annealing
Annealing can be done in two types
i. Low temperature annealing (or) process annealing
ii. High temperature annealing 9or) full annealing
Low temperature annealing (or)process annealing
It involves in heating steel to a temperature below the lower critical point followed by slow cooling
Purpose
1. It improves mashinability by reliving the internal stress or internal strain
2. It increases ductility and shock resistance
3. It reduce hardness
(i) High temperature annealing (or) fault annealing
It involves in heating to a temperature about 30 to 50⁰C above the higher critical temperature and holding it at that temperature for sufficient time to allow the internal changes to take place and then cooled room
temperature
The approximate annealing temperature of various grades of carbon steel
are
1. Mild steel=840-870⁰c
2. Medium carbon steel=780-840⁰c
3. High carbon steel=760-780⁰c
Purpose
1. It increases the ductility and machinability
2. It makes the steel softer, together with an appreciable increases in its toughness
2.Hardening (or) quenching
· It is the process of heating steel beyond the critical temperature and then suddenly cooling it either in oil or brine water or some other fluid.
· The faster the rate of cooling harder will be the steel produced.
· Medium and high carbon steel can be hardened but low carbon steel cannot hardened
Purpose
1. It increases its resistance to wear ability ,to cut other metal and strength .
2. It increases abrasion resistance.
3. Used for making cutting tools.
3. TEMPERING
· It is the process of heating the already hardened steel to a temperature lower than its own hardening temperature & then cooling it slowly.
· The reheating controls the development of the final properties
· Thus,
(a)For retaining strength & hardness, reheating temperature should not exceed 400⁰C.
(b) For developing better ductility & toughness, reheating temperature should be within 400-600⁰C.
Purpose
1. It removes stress &strains that might have developed during quenching.
2. Increased toughness & ductility.
3. Used for cutting tools like blade,cutters etc.
4. NORMALISING
It is the purpose of heating steel to a definite temperature (above its higher critical temperature) & allowing it to cool gradually in air. Purpose
1. Recovers homogeneity
2. Refines grains.
3. Removes internal stresses
4. Increases toughness
5. Used in engineering works
NOTE: The difference between normalised & annealed steel are
1. A normaled steel will not be as soft as annealed steel.
2. Also normalizing takes much lesser time than annealing.
5.CARBURIZING
· The mild steel article is taken in a cast iron box within containing small pieces of charcoal(carbon material).
· It is heated to about 900 to 950⁰C & allow it for sufficient time,so that the carbon is absorbed to required depth .
· The article is then allowed to cool slowly within the box itself.
· The outer skin of the article is converted into high carbon steel containing
about 0.8 to 1.2% carbon. Purpose
To produce hard surface on steel article
6.NITRIDING
· Nitriding is the process of heating the metal alloy in presence of ammonia to about 550⁰C.
· The nitrogen (obtained by the dissociation of ammonia) combines with the surface of the alloy to form hard nitride.
Purpose
To get super-hard surface.
Comments are closed.