Ask any member of the oil and gas (O&G) industry what their main concern is and the most common response is occupational health and safety. Any business is vulnerable to an accident; however, the O&G industry is a particularly risky business, handling flammable and, in some cases, toxic fluids and finished products. The exploration/production, transmission/distribution, and refinement of crude oil and natural gas require complicated processing equipment and operations. Because the energy industry is inherently exposed to numerous risks, safety is the highest priority. More importantly, good safety programs contribute and support sustainable growth for O&G companies.
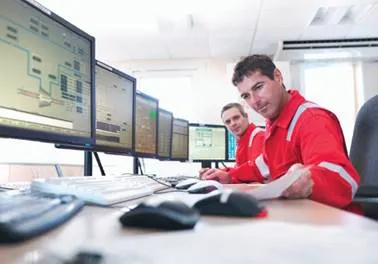
Continuous improvement needed
It is not a surprise that sustainability ratings are heavily weighted on safety and environmental performances. Following catastrophic events, such as the toxic methyl isocyanate (MIC) gas release from Union Carbide’s pesticide facility in Bhopal, India, the Responsible Care movement focused tremendous efforts and standards on promoting facility safety for the chemical and energy industries. National governments passed legislation defining safety requirements and conduct for heavy manufacturing industries, including O&G. Yet, 30 years later, accidents still happen, such as the Deep Water Horizon oil rig explosion and crude oil release in 2010 and the BP Texas City refinery vapor-cloud explosion in 2005.
Major O&G facilities are billion dollar investments. The design of O&G platforms and refineries includes equipment and control systems to protect the investment (assets), workers, and the environment. Preventing fires and catastrophic releases is a huge concern. Leaks of hydrocarbons within a facility or rig can quickly escalate and become a catastrophe event.
Safety programs are complex
Safety is not a one-time action. Successful safety programs include:
· Employee and contractor training
· Complete and accessible unit operation procedures and practices
· Equipment conditioning and maintenance programs
· Incident (accident) investigation and follow-up
· Lifecycle process/equipment design and management.
New generation instrumentation and control equipment have automated O&G operations. Yet, even with the latest monitoring and sensor systems, risks from accidents or releases still exist. Safe operations and protocols are important; failures in such systems impact human life, production (economic) assets, and the environment.
Making progress
Innovative technologies have transformed how companies collect and distribute process information. Next-generation devices now include “intelligence” as part of their protocol that check/confirm the health of field devices, especially sensors and instrumentation involved in alarm and emergency shutdown (ESD) systems. New field “intelligence” can report malfunctions before the device fails. The merging of digitalization and wireless technologies enable companies to have real-time data on process systems and critical equipment.
For example, new sensors and wireless technologies now monitor critical equipment and process conditions including temperature, pressure, flow rates, and more. Platform or facility operations rely on such equipment to control systems and the process unit. Now, data is collected, analyzed, converted into information, and mined into actions. Safer operations are possible through the enhanced connectivity and the flow of information.
ESD systems and fire protection
For the O&G industry, the facilities’ safety systems are the last defense against catastrophic events. EDS and fire and gas monitoring systems must perform near 100% with zero failures. The key to EDS and fire and gas systems is the architecture and smart field devices and sensors used to perform corrective actions. Wireless technologies enable locating sensors at critical locations without the burden and cost of physical connections.
Maintenance is part of safety programs
Just as wireless sensors alert abnormal process conditions, they can be effectively used to detect problems in critical process equipment. The trend to build leaner O&G facilities has eliminated spare equipment installations. The operation of critical pumps and compressors can be the determining factor in preventing unscheduled downtime or reduced operating rates—both negatively affect profits of the process unit and facility. ESD events create situations in which operating procedure mistakes can escalate into a major incident. Asset management and maintenance programs strive to prevent unscheduled downtime and accidental flammable product leaks and releases. Leveraging collected information on plant assets and process conditions enables O&G companies to run their operations at the highest level while maintaining a safe environment for workers, the community, and the environment.
Training
“We all go home.” This phrase was previously used in an advertising program for an alkylation technology. The message stresses that comprehensive efforts are needed so that all workers return home to their families every day. Quality training programs are crucial elements for any O&G operation. Virtual 3-D reality simulation models have radically change the way operating staff are trained. Innovative models replicate the actual process equipment and control boards. Using such models and graphics, new and experienced operators can effectively practice operation actions in a virtual world. Here, they witness the consequences from improper actions in a completely safe environment. In addition, the models allow practice of abnormal events to fine-tune proper actions and collect best practices. O&G facilities are constantly undergoing changing conditions; thus, training must be dynamic and adapting to new situations. Likewise, high-fidelity virtual models can expose potential crisis situations before they actually occur.
EYESIM™ is a high-fidelity training simulator that models an exact replica of the plant.
Preparation and prevention
Safety is always about preparation and prevention. Preparation involves the design of the unit and equipment plus the monitoring and control systems. New architectures enable linking process monitoring devices to edge-of-control systems. In addition, advanced apps and analytics combine hardware, software, and control devices. Improved monitoring of process and equipment contribute greatly to safer working conditions and protecting plant assets, workers, and the environment. Likewise, minimizing equipment failures and reducing unscheduled downtime improves safety conditions, profits, and sustainability performance. Proactive asset/maintenance programs keep equipment operating under manufacturer recommended conditions.
New attitude on safety
Safety excellence is reframing from zero accidents to sustainable and repeatable value.1 The new attitude on safety goes beyond reducing reportable worker injuries and releases. Improved sustainable performance includes safety and environmental programs.
Effective safety programs merge people, procedure/practices, and process data into enterprise-wide standard operating methods. Such systems are supported by top management to get buy-in from employees and contractors. Remember: Safety is not a one-time action; it is a daily attitude for all.