Natural gas that is mainly methane cannot be compressed to liquid state at normal ambient temperature. Except for special uses such as compressed natural gas (CNG), the only practical solution to long distance gas transportation when a pipeline is not available or economical is to produce LNG at -162 °C. This requires one or more cooling stages. Cooling work consumes 6-10% of the energy to be transported. Special insulated tank LNG carriers are required for transportation, and at the receiving end, a regasification terminal heats the LNG to vaporization for pipeline distribution.
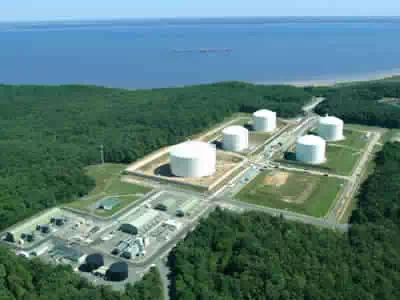
Refining
Refining aims to provide a defined range of products according to agreed specifications. Simple refineries use a distillation column to separate crude into fractions, and the relative quantities are directly dependent on the crude used. Therefore, it is necessary to obtain a range of crudes that can be blended to a suitable feedstock to produce the required quantity and quality of end products The economic success of a modern refinery depends on its ability to accept almost any available crude. With a variety of processes such as cracking, reforming, additives and blending, it can provide product in quantity and quality to meet market demand at premium prices. The refinery operations often include product distribution terminals for dispensing product to bulk customers such as airports, gasoline stations, ports and industries.
Petrochemical
Chemicals derived from petroleum or natural gas – petrochemicals – are an essential part of today’s chemical industry. Petrochemical plants produce thousands of chemical compounds. The main feedstock is natural gas, condensates (NGL) and other refinery by-products such as naphtha, gasoil, and benzene. Petrochemical plants are divided into three main primary product groups according to their feedstock and primary petrochemical product:
Olefins include ethylene, propylene, and butadiene. These are the main sources of plastics (polyethylene, polyester, PVC), industrial chemicals and synthetic rubber.
Aromatics include benzene, toluene, and xylenes, which also are a source of plastics (polyurethane, polystyrene, acrylates, nylon), as well as synthetic detergents and dyes.
Synthesis gas (syngas) is formed by steam reforming between methane and steam to create a mixture of carbon monoxide and hydrogen. It is used to make ammonia, e.g., for fertilizer urea, and methanol as a solvent and chemical intermediary. Syngas is also feedstock for other processes such as the Fischer–Tropsch process that produces synthetic diesel.
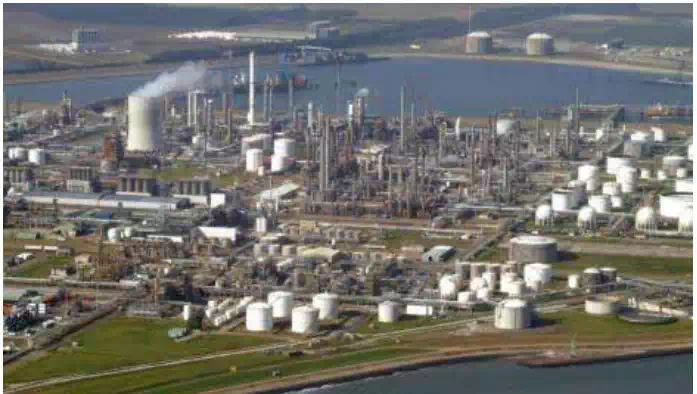
Photo: DOW, Terneusen, Netherlands
Reservoir and wellheads
There are three main types of conventional wells. The most common is an oil well with associated gas. Natural gas wells are drilled specifically for natural gas, and contain little or no oil. Condensate wells contain natural gas, as well as a liquid condensate. This condensate is a liquid hydrocarbon mixture that is often separated from the natural gas either at the wellhead, or during the processing of the natural gas. Depending on the well type, completion may differ slightly. It is important to remember that natural gas, being lighter than air, will naturally rise to the surface of a well. Consequently, lifting equipment and well treatment are not necessary in many natural gas and condensate wells, while for oil wells, many types of artificial lift may be installed, particularly as the reservoir pressure falls during years of production. There is no distinct transition from conventional to unconventional oil and gas production. Lower porosity (tighter reservoirs) and varying maturity create a range of shale oil and gas, tight gas, heavy oil, etc., that is simply an extension of the conventional domain.
Comments are closed.