Well planning is perhaps the most demanding aspect of drilling engineering. It requires the integration of engineering principles, corporate or personal philosophies, and experience factors. Although well planning methods and practices may vary within the drilling industry, the end result should be a safely drilled, minimum-cost hole that satisfies the reservoir engineer’s requirements for oil/gas production.
Qualities of a well planner
The skilled well planners normally have three common traits:
· They are experienced drilling personnel who understand how all aspects of the drilling operation must be integrated smoothly.
· They utilize available engineering tools, such as computers and third-party recommendations, to guide the development of the well plan.
· they usually have an investigative characteristic that drives them to research and review every aspect of the plan in an effort to isolate and remove potential problem areas.
Objective of well planning
The objective of well planning is to formulate from many variables a program for drilling a well that has the following characteristics:
· Safe
· Minimum cost
· Usable
Unfortunately, it is not always possible to accomplish these objectives on each well because of constraints based on:
· Geology
· Drilling equipment
· Temperature
· Casing limitations
· Hole sizing
· Budget
Safety
Safety should be the highest priority in well planning. Personnel considerations must be placed above all other aspects of the plan. In some cases, the plan must be altered during the course of drilling the well when unforeseen drilling problems endanger the crew. Failure to stress crew safety has resulted in loss of life and burned or permanently crippled individuals.
The second priority involves the safety of the well. The well plan must be designed to minimize the risk of blowouts and other factors that could create problems. This design requirement must be adhered to rigorously in all aspects of the plan. Example 1 illustrates a case in which this consideration was neglected in the earliest phase of well planning, which is data collection.
Minimum cost
A valid objective of the well-planning process is to minimize the cost of the well without jeopardizing the safety aspects. In most cases, costs can be reduced to a certain level as additional effort is given to the planning (Fig. 1). It is not noble to build “steel monuments” in the name of safety, if the additional expense is not required. On the other hand, funds should be spent as necessary to develop a safe system.
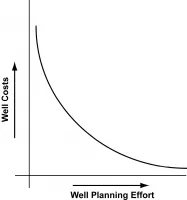
Fig. 1—Well costs can be reduced dramatically if proper well planning is implemented.
Usable holes
Drilling a hole to the target depth is unsatisfactory if the final well configuration is not usable. In this case, the term “usable” implies the following:
· The hole diameter is sufficiently large so an adequate completion can be made.
· The hole or producing formation is not irreparably damaged.
This requirement of the well planning process can be difficult to achieve in abnormal-pressure, deep zones that can cause hole-geometry or mud problems.
Well-type classification
The drilling engineer is required to plan a variety of well types, including:
· Wildcats
· Exploratory holes
· Step-outs
· Infills
· Re-entries
Generally, wildcats require more planning than the other types. Infill wells and re-entries require minimum planning in most cases.
Wildcats are drilled where little or no known geological information is available. The site may have been selected because of wells drilled some distance from the proposed location but on a terrain that appeared similar to the proposed site. The term “wildcatter” was originated to describe the bold frontiersman willing to gamble on a hunch.
Rank wildcats are seldom drilled in today’s industry. Well costs are so high that gambling on wellsite selection is not done in most cases. In addition, numerous drilling prospects with reasonable productive potential are available from several sources. However, the romantic legend of the wildcatter will probably never die. Characteristics of various well types are shown in Table 1.
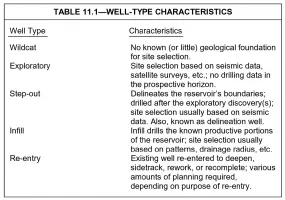
Table 1-Well-Type Characteristics
Formation pressure
The formation, or pore, pressure encountered by the well significantly affects the well plan. The pressures may be normal, abnormal (high), or subnormal (low).
Normal-pressure wells generally do not create planning problems. The mud weights are in the range of 8.5 to 9.5 lbm/gal. Kicks- and blowout-prevention problems should be minimized but not eliminated altogether. Casing requirements can be stringent even in normal-pressure wells deeper than 20,000 ft because of tension/collapse design constraints.
Subnormal-pressure wells may require setting additional casing strings to cover weak or low-pressure zones. The lower-than-normal pressures may result from geological or tectonic factors or from pressure depletion in producing intervals. The design considerations can be demanding if other sections of the well are abnormal pressured.
Abnormal pressures affect the well plan in many areas, including:
· Casing and tubing design
· Mud-weight and type-selection
· Casing-setting-depth selection
· Cement planning
In addition, the following problems must be considered as a result of high formation pressures:
· Kicks and blowouts
· Differential-pressure pipe sticking
· Lost circulation resulting from high mud weights
· Heaving shale
Well costs increase significantly with geopressures.
Because of the difficulties associated with well planning for high-pressure exploratory wells, many design criteria, publications, and studies have been devoted to this area. The amount of effort expended is justified. Unfortunately, the drilling engineer still must define the planning parameters that can be relaxed or modified when drilling normal-pressure holes or well types such as step-outs or infills.
Planning costs
The costs required to plan a well properly are insignificant in comparison to the actual drilling costs. In many cases, less than U.S. $1,000 is spent in planning a U.S. $1 million well. This represents 1/10 of 1%; of the well costs.
Unfortunately, many historical instances can be used to demonstrate that well planning costs were sacrificed or avoided in an effort to be cost conscious. The end result often is a final well cost that exceeds the amount required to drill the well, if proper planning had been exercised. Perhaps the most common attempted shortcut is to minimize data-collection work. Although good data can normally be obtained for small sums, many well plans are generated without the knowledge of possible drilling problems. This lack of expenditure in the early stages of the planning process generally results in higher-than-anticipated drilling costs.
Well planning process
Well planning is an orderly process. It requires that some aspects of the plan be developed before designing other items. For example, the mud density plan must be developed before the casing program because mud weights have an impact on pipe requirements (Fig. 2).
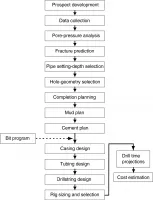
Fig. 2—Flow path for well planning.
Bit programming can be done at any time in the plan after the historical data have been analyzed. The bit program is usually based on drilling parameters from offset wells. However, bit selection can be affected by the mud plan [i.e., the performance of polycrystalline-diamond (PCD) bits in oil muds]. Casing-drift-diameter requirements may control bit sizing.
Casing and tubing should be considered as an integral design. This fact is particularly valid for production casing. A design criterion for tubing is the drift diameter of the production casing, whereas the packer-to-tubing forces created by the tubing’s tendencies for movement can adversely affect the production casing. Unfortunately, these calculations are complex and often neglected.
The completion plan must be visualized reasonably early in the process. Its primary effect is on the size of casing and tubing to be used if oversized tubing or packers are required. In addition, the plan can require the use of high-strength tubing or unusually long seal assemblies in certain situations.
Comments are closed.