Production phase aims to the recovery of the reservoir fluids to surface followed by their processing.
All production and maintenance activities are carried out to meet strict safety and environmental policies and procedures.
During the production phase it is necessary to:
- control production and injection to meet up approved plans for volumes and quality of products
- monitor and record all data to manage the reservoir, wells and facilities
The production phase begins with the first commercial volumes of hydrocarbons (“first oil”) flowing through the wellhead – this establishes a fundamental turning point from a cash flow stand point.
From now on, cash is generated and can be used to pay back the previous investments, or may be made available for new projects (ex. new exploration…).
The development and production planning are based on the expected production profile which are strongly dependent on the reservoir drive mechanism.
It is the forecasted production profile that will determine the size of facilities required to treat and disposes the fluids and the number and phasing of wells to be drilled.
A typical production profile is made up by three phases:
- Build-up period
- during this period production wells are progressively brought on flow
- Plateau period
- a constant production rate is mantained
- Decline period
- all producers show declining of production rates
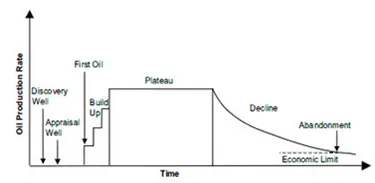
Typical field production profile
The mode of operations and maintenance required are specified in the field development plan.
It is necessary to deliver product at the required rate and quality and therefore, the product quality specification and contract terms guide the activities of the production operations.
The “product” quality is not limited to oil and gas, but also to other fluid/byproduct streams.
The process and facilities engineers design
- the equipment for a range of capacities (maximum throughputs)
- the type of operation and maintenance
The processing plants are designed to treat specific types of hydrocarbon according to their characteristics.
The recovered fluids are processed for technical, safety and economic reasons
By processing the produced fluids, it is possible to
- remove any fluid non-hydrocarbon components (water, carbon dioxide, hydrogen sulphide, nitrogen, etc.) or solids
- bring the hydrocarbons quality up to the required specifications
Gas processing may include
- separation
- dehydration for the removal of water carried out through various systems such as refrigeration, adsorption and absorption
- condensate removal carried out by means of refrigeration and adsorption
- desulphurisation-decarbonation to remove hydrogen sulphide and carbon dioxide (when found in intolerable quantities)
Crude oil processing may include
- gas-oil separation
- water-oil separation
- desalting to eliminate the saline content
- desulphurization to remove the hydrogen sulphide content
- stabilization to meet the required standards
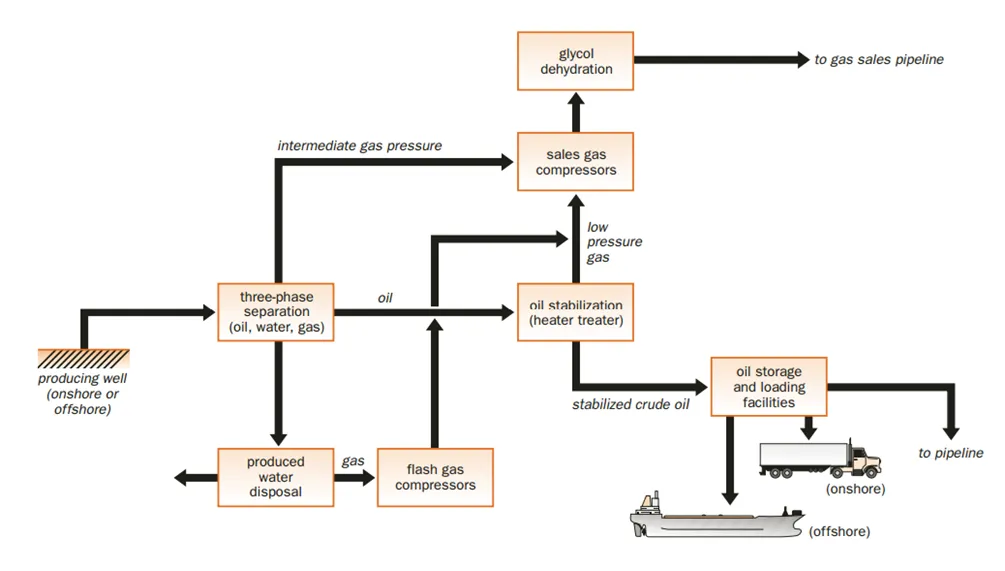
Typical Crude Oil Processing
During production, monitoring and control of the production processes is performed by a combination of instrumentation and control equipment which
- increase production rates
- reduce operating expenditure
- reduce capital expenditure
- increase safety
- improve environmental protection
Waste disposal is another important aspect of the production process and it should cover all effluent streams.
The treatment of these products and waste is discussed jointly with the Environment department, process and facilities engineers.
An oil and gas processing plant include the utilities systems which do not take part to the processes but support production operations
Utility systems include
- power system (fuel gas and diesel)
- water and potable water treatment system
- chemicals and lubrication oils alarm
- shut-down system
- fire protection and fire fighting system
- instrument/utility air system, etc
The necessary control and monitoring of processing operations is managed from the control room, which is a dedicated structure where operators perform plant operations monitor and control using sophisticated and automatic control systems in a safe and efficient manner.
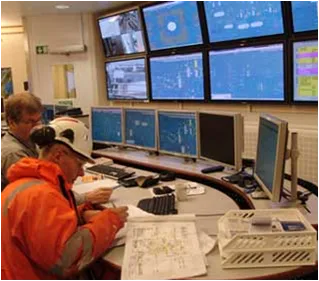
Operators in a processing plant control room
Comments are closed.