Although included under the separation processes, catalytic dewaxing is actually a low-severity conversion process involving a selective catalytic cracking of n-paraffins. Because of removing wax (long chain n-paraffins) by chemical reaction, the process is called dewaxing. The selective cracking of n-alkanes takes place in the pores of molecular sieve catalysts (zeolites) with pore openings in the order of 0.6nm, which keep i-paraffins out because of their larger size due to branching in the hydrocarbon skeleton, as shown in Figure 5.13. This selective cracking increases the ratio of i-paraffins to n-paraffins in the product and lowers its pour point. Hydrogen is introduced along with the feed to prevent coking on the catalyst surfaces (Figure 5.14). The cracking of n-paraffins produces distillate fuels such as gasoline as a by-product from catalytic dewaxing.
The advantages of catalytic dewaxing include:
· production of lube base stock with lower pour point and in higher yield compared to the product obtained from solvent dewaxing. Low yield from solvent dewaxing results from the difficulty of separating the oil from the wax;
· lower capital investment;
· good product stability;
· flexibility to produce both lube oil base stock and light distillates.
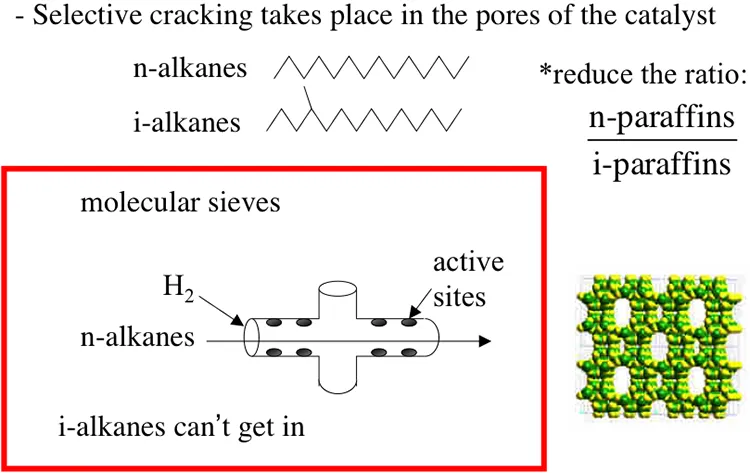
Figure 5.13. Chemistry of catalytic dewaxing inside molecular sieving zeolites, e.g., mordenite, the structure of which is shown in the figure.
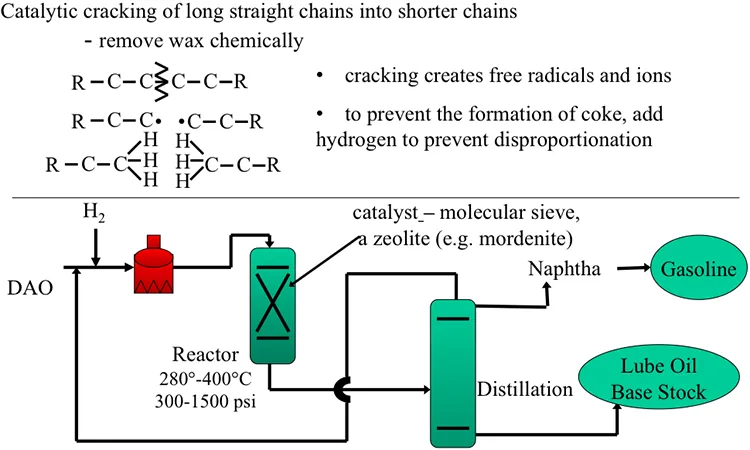
Figure 5.14. Catalytic dewaxing process.
Comments are closed.