General Profile
Petroleum refining begins with the distillation, or fractionation, of crude oils into separate hydrocarbon groups. The resultant products are directly related to the characteristics of the crude oil being processed. Most of these products of distillation are further converted into more useable products by changing their physical and molecular structures through cracking, reforming and other conversion processes. These products are subsequently subjected to various treatment and separation processes, such as extraction, hydrotreating and sweetening, in order to produce finished products. Whereas the simplest refineries are usually limited to atmospheric and vacuum distillation, integrated refineries incorporate fractionation, conversion, treatment and blending with lubricant, heavy fuels and asphalt manufacturing; they may also include petrochemical processing.
The first refinery, which opened in 1861, produced kerosene by simple atmospheric distillation. Its by-products included tar and naphtha. It was soon discovered that high-quality lubricating oils could be produced by distilling petroleum under vacuum. However, for the next 30 years, kerosene was the product consumers wanted most. The two most significant events which changed this situation were:
· the invention of the electric light, which decreased the demand for kerosene
· the invention of the internal-combustion engine, which created a demand for diesel fuel and gasoline (naphtha).
With the advent of mass production and the First World War, the number of gasoline-powered vehicles increased dramatically, and the demand for gasoline grew accordingly. However, only a certain amount of gasoline could be obtained from crude oil through atmospheric and vacuum distillation processes. The first thermal cracking process was developed in 1913. Thermal cracking subjected heavy fuels to both pressure and intense heat, physically breaking their large molecules into smaller ones, producing additional gasoline and distillate fuels. A sophisticated form of thermal cracking, visbreaking, was developed in the late 1930s to produce more desirable and valuable products.
As higher-compression gasoline engines were developed, there was a demand for higher-octane gasoline with better anti-knock characteristics. The introduction of catalytic cracking and poly- merization processes in the mid- to late 1930s met this demand by providing improved gasoline yields and higher octane numbers. Alkylation, another catalytic process, was developed in the early 1940s to produce more high-octane aviation gasoline and petrochemical feedstocks, the starting materials, for explosives and synthetic rubber. Subsequently, catalytic isomerization was developed to convert hydrocarbons to produce increased quantities of alkylation feedstocks.
Following the Second World War, various reforming processes were introduced which improved gasoline quality and yield, and produced higher-quality products. Some of these involved the use of catalysts and/or hydrogen to change molecules and remove sulphur. Improved catalysts, and process methods such as hydrocracking and reforming, were developed throughout the 1960s to increase gasoline yields and improve anti-knock characteristics. These catalytic processes also produced molecules with a double bond (alkenes), forming the basis of the modern petrochemical industry.
The numbers and types of different processes used in modern refineries depend primarily on the nature of the crude feedstock and finished product requirements. Processes are also affected by economic factors including crude costs, product values, availability of utilities and transportation. The chronology of the introduction of various processes is given in table 1.
Table 1. Summary of the history of refining processing
Year | Process name | Process purpose | Process by-products |
1862 | Atmospheric distillation | Produce kerosene | Naphtha, tar, etc. |
1870 | Vacuum distillation | Lubricants (original) Cracking feedstocks (1930s) | Asphalt, residual Coker feedstocks |
1913 | Thermal cracking | Increase gasoline | Residual, bunker fuel |
1916 | Sweetening | Reduce sulphur and odour | Sulphur |
1930 | Thermal reforming | Improve octane number | Residual |
1932 | Hydrogenation | Remove sulphur | Sulphur |
1932 | Coking | Produce gasoline base stocks | Coke |
1933 | Solvent extraction | Improve lubricant viscosity index | Aromatics |
1935 | Solvent dewaxing | Improve pour point | Waxes |
1935 | Catalytic polymerization | Improve gasoline yield and octane number | Petrochemical feedstocks |
1937 | Catalytic cracking | Higher octane gasoline | Petrochemical feedstocks |
1939 | Visbreaking | Reduce viscosity | Increased distillate, tar |
1940 | Alkylation | Increase gasoline octane and yield | High-octane aviation gasoline |
1940 | Isomerization | Produce alkylation feedstock | Naphtha |
1942 | Fluid catalytic cracking | Increase gasoline yield and octane | Petrochemical feedstocks |
1950 | Deasphalting | Increase cracking feedstock | Asphalt |
1952 | Catalytic reforming | Convert low-quality naphtha | Aromatics |
1954 | Hydrodesulphurization | Remove sulphur | Sulphur |
1956 | Inhibitor sweetening | Remove mercaptan | Disulphides |
1957 | Catalytic isomerization | Convert to molecules with high octane number | Alkylation feedstocks |
1960 | Hydrocracking | Improve quality and reduce sulphur | Alkylation feedstocks |
1974 | Catalytic dewaxing | Improve pour point | Wax |
1975 | Residual hydrocracking | Increase gasoline yield from residual | Heavy residuals |
Basic refining processes and operations
Petroleum refining processes and operations can be classified into the following basic areas: separation, conversion, treatment, formulating and blending, auxiliary refining operations and refining non-process operations. See figure 1 for a simplified flow chart.
Figure 1. Refinery process chart
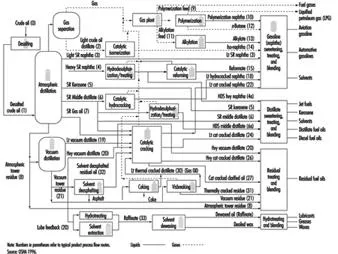
Separation. Crude oil is physically separated by fractionation in atmospheric and vacuum distillation towers, into groups of hydrocarbon molecules with various boiling-point ranges, called “fractions” or “cuts”.
Conversion. Conversion processes used to change the size and/or structure of hydrocarbon molecules include:
· decomposition (dividing) by hydro-, thermal and catalytic cracking, coking and visbreaking
· unification (combining) through alkylation and polymerization
· alteration (rearranging) with isomerization and catalytic reforming
· treatment.
Since the beginning of refining, various treatment methods have been used to remove non-hydrocarbons, impurities and other constituents that adversely affect the performance properties of finished products or reduce the efficiency of the conversion processes. Treatment involves both chemical reactions and physical separation, such as dissolving, absorption or precipitation, using a variety and combination of processes. Treatment methods include removing or separating aromatics and naphthenes, as well as removing impurities and undesirable contaminants. Sweetening compounds and acids are used to desulphurize crude oil before processing, and to treat products during and after processing. Other treatment methods include crude desalting, chemical sweetening, acid treating, clay contacting, hydrodesulphurizing, solvent refining, caustic washing, hydrotreating, drying, solvent extraction and solvent dewaxing.
Formulating and blending is the process of mixing and combining hydrocarbon fractions, additives and other components to produce finished products with specific desired performance properties.
Auxiliary refining operations. Other refinery operations which are required to support hydrocarbon processing include light ends recovery; sour water stripping; solid waste, waste water and process water treatment and cooling; hydrogen production; sulphur recovery; and acid and tail gas treatment. Other process functions are providing catalysts, reagents, steam, air, nitrogen, oxygen, hydrogen and fuel gases.
Refinery non-process facilities. All refineries have a multitude of facilities, functions, equipment and systems which support the hydrocarbon process operations. Typical support operations are heat and power generation; product movement; tank storage; shipping and handling; flares and relief systems; furnaces and heaters; alarms and sensors; and sampling, testing and inspecting. Non-process facilities and systems include firefighting, water and protection systems, noise and pollution controls, laboratories, control rooms, warehouses, maintenance and administrative facilities.
Major Products of Crude Oil Refining
Petroleum refining has evolved continuously in response to changing consumer demand for better and different products. The original process requirement was to produce kerosene as a cheaper and better source of fuel for lighting than whale oil. The development of the internal combustion engine led to the production of benzene, gasoline and diesel fuels. The evolution of the airplane created a need for high-octane aviation gasoline and jet fuel, which is a sophisticated form of the original refinery product, kerosene. Present-day refineries produce a variety of products, including many which are used as feedstocks for cracking processes and lubricant manufacturing, and for the petrochemical industry. These products can be broadly classified as fuels, petrochemical feedstocks, solvents, process oils, lubricants and special products such as wax, asphalt and coke. (See table 2.)
Table 2. Principal products of crude oil refining
Hydrocarbon gases | Uses |
Liquified gases | Cooking and industrial gas Motor fuel gas Illuminating gas Ammonia Synthetic fertilizer Alcohols Solvents and acetone Plasticizers Resins and fibres for plastics and textiles Paints and varnish |
Chemical industry feedstock | Rubber products |
Carbon black | Printing inks Rubber industry |
Light distillates | |
Light naphthas | Olefins Solvents and diluents Extraction solvents Chemical industry feedstocks |
Intermediate naphthas | Aviation and motor gasoline Dry-cleaning solvents |
Heavy naphthas | Military jet fuel Jet fuel and kerosene Tractor fuel |
Gas oil | Cracking stock Heating oil and diesel fuel Metallurgical fuel Absorber oil—benzene and gasoline recovery |
Heavy distillates | |
Technical oils | Textile oils Medicinal oils and cosmetics White oil—food industry |
Lubricating oils | Transformer and spindle oils Motor and engine oils Machine and compressor oils Turbine and hydraulic oils Transmission oils Equipment and cable insulation oils Axle, gear and steam engine oils Metal treating, cutting and grinding oils Quenching and rust inhibitor oils Heat transfer oils Lubricating greases and compounds Printing ink oils |
Paraffin wax | Rubber industry Pharmaceuticals and cosmetics Food and paper industries Candles and matches |
Residues | |
Petrolatum | Petroleum jelly Cosmetics Rust inhibitors and lubricants Cable coating compounds |
Residual fuel oil | No. 6 boiler and process fuel oil |
Asphalts | Paving asphalt Roofing materials Asphaltic lubricants Insulating and foundation protection Waterproof paper products |
Refinery by-products | |
Coke | Electrodes and fuel |
Sulphonates | Emulsifiers |
Sulphuric acid | Synthetic fertilizer |
Sulphur | Chemicals |
Hydrogen | Hydrocarbon reformation |
A number of chemicals are used in, or formed as a result of, hydrocarbon processing. A brief description of those which are specific and pertinent to refining follows:
Sulphur Dioxide
Flue gas from burning high-sulphur-content fuels usually contains high levels of sulphur dioxide, which usually is removed by water scrubbing.
Caustics
Caustics are added to desalting water to neutralize acids and reduce corrosion. Caustics are also added to desalted crude in order to reduce the amount of corrosive chlorides in the tower overheads. They are used in refinery treating processes to remove contaminants from hydrocarbon streams.
Nitrogen oxides and carbon monoxide
Flue gas contains up to 200 ppm of nitric oxide, which reacts slowly with oxygen to form nitrogen dioxide. Nitric oxide is not removed by water scrubbing, and nitrogen dioxide can dissolve in water to form nitrous and nitric acid. Flue gas normally contains only a slight amount of carbon monoxide, unless combustion is abnormal.
Hydrogen sulphide
Hydrogen sulphide is found naturally in most crude oils and is also formed during processing by the decomposition of unstable sulphur compounds. Hydrogen sulphide is an extremely toxic, colourless, flammable gas which is heavier than air and soluble in water. It has a rotten egg odour which is discernible at concentrations well below its very low exposure limit. This smell cannot be relied upon to provide adequate warning as the senses are almost immediately desensitized upon exposure. Special detectors are required to alert workers to the presence of hydrogen sulphide, and proper respiratory protection should be used in the presence of the gas. Exposure to low levels of hydrogen sulphide will cause irritation, dizziness and headaches, while exposure to levels in excess of the prescribed limits will cause nervous system depression and eventually death.
Sour water
Sour water is process water which contains hydrogen sulphide, ammonia, phenols, hydrocarbons and low-molecular-weight sulphur compounds. Sour water is produced by steam stripping hydrocarbon fractions during distillation, regenerating catalyst, or steam stripping hydrogen sulphide during hydrotreating and hydrofinishing. Sour water is also generated by the addition of water to processes to absorb hydrogen sulphide and ammonia.
Sulphuric acid and hydrofluoric acid
Sulphuric acid and hydrofluoric acid are used as catalysts in alkylation processes. Sulphuric acid is also used in some of the treatment processes.
Solid catalysts
A number of different solid catalysts in many forms and shapes, from pellets to granular beads to dusts, made of various materials and having various compositions, are used in refining processes. Extruded pellet catalysts are used in moving and fixed bed units, while fluid bed processes use fine, spherical particulate catalysts. Catalysts used in processes which remove sulphur are impregnated with cobalt, nickel or molybdenum. Cracking units use acid-function catalysts, such as natural clay, silica alumina and synthetic zeolites. Acid-function catalysts impregnated with platinum or other noble metals are used in isomerization and reforming. Used catalysts require special handling and protection from exposures, as they may contain metals, aromatic oils, carcinogenic polycyclic aromatic compounds or other hazardous materials, and may also be pyrophoric.
Fuels
The principal fuel products are liquefied petroleum gas, gasoline, kerosene, jet fuel, diesel fuel and heating oil and residual fuel oils. Liquefied petroleum gas (LPG), which consists of mixtures of paraffinic and olefinic hydrocarbons such as propane and butane, is produced for use as a fuel, and is stored and handled as liquids under pressure. LPG has boiling points ranging from about –74 °C to
+38 °C, is colourless, and the vapours are heavier than air and extremely flammable. The important qualities from an occupational health and safety perspective of LPGs are vapour pressure and control of contaminants.
Gasoline. The most important refinery product is motor gasoline, a blend of relatively low-boiling hydrocarbon fractions, including reformate, alkylate, aliphatic naphtha (light straight-run naphtha), aromatic naphtha (thermal and catalytic cracked naphtha) and additives. Gasoline blending stocks have boiling points which range from ambient temperatures to about 204 °C, and a flashpoint below –40 °C. The critical qualities for gasoline are octane number (anti-knock), volatility (starting and vapour lock) and vapour pressure (environmental control). Additives are used to enhance gasoline performance and provide protection against oxidation and rust formation. Aviation gasoline is a high-octane product, specially blended to perform well at high altitudes. Tetra ethyl lead (TEL) and tetra methyl lead (TML) are gasoline additives which improve octane ratings and anti-knock performance. In an effort to reduce lead in automotive exhaust emissions, these additives are no longer in common use, except in aviation gasoline.
Ethyl tertiary butyl ether (ETBE), methyl tertiary butyl ether (MTBE), tertiary amyl methyl ether (TAME) and other oxygenated compounds are used in lieu of TEL and TML to improve unleaded gasoline anti-knock performance and reduce carbon monoxide emissions. Jet fuel and kerosene. Kerosene is a mixture of paraffins and naphthenes with usually less than 20% aromatics. It has a flashpoint above 38 °C and a boiling range of 160 °C to 288 °C, and is used for lighting, heating, solvents and blending into diesel fuel. Jet fuel is a middle distillate kerosene product whose critical qualities are freezepoint, flashpoint and smokepoint. Commercial jet fuel has a boiling range of about 191 °C to 274 °C, and military jet fuel from 55 °C to 288 °C.
Distillate fuels. Diesel fuels and domestic heating oils are light-coloured mixtures of paraffins, naphthenes and aromatics, and may contain moderate quantities of olefins. Distillate fuels have flashpoints above 60 °C and boiling ranges of about 163 °C to 371 °C, and are often hydrodesulphurized for improved stability. Distillate fuels are combustible and when heated may emit vapours which can form ignitable mixtures with air. The desirable qualities required for distillate fuels include controlled flash- and pourpoints, clean burning, no deposit formation in storage tanks, and a proper diesel fuel cetane rating for good starting and combustion.
Residual fuels. Many ships and commercial and industrial facilities use residual fuels or combinations of residual and distillate fuels, for power, heat and processing. Residual fuels are dark- coloured, highly viscous liquid mixtures of large hydrocarbon molecules, with flashpoints above 121 °C and high boiling points. The critical specifications for residual fuels are viscosity and low sulphur content (for environmental control).
Health and safety considerations
The primary safety hazard of LPG and gasoline is fire. The high volatility and high flammability of the lower-boiling-point products allows vapours to evaporate readily into air and form flammable mixtures which can be easily ignited. This is a recognized hazard that requires specific storage, containment and handling precautions, and safety measures to assure that releases of vapours and sources of ignition are controlled so that fires do not occur. The less volatile fuels, such as kerosene and diesel fuel, should be handled carefully to prevent spills and possible ignition, as their vapours are also combustible when mixed with air in the flammable range. When working in atmospheres containing fuel vapours, concentrations of highly volatile, flammable product vapours in air are often restricted to no more than 10% of the lower flammable limits (LFL), and concentrations of less volatile, combustible product vapours to no more than 20% LFL, depending on applicable company and government regulations, in order to reduce the risk of ignition.
Although gasoline vapour levels in air mixtures are typically maintained below 10% of the LFL for safety purposes, this concentration is considerably above the exposure limits to be observed for health reasons. When inhaled, small amounts of gasoline vapour in air, well below the lower flammable limit, can cause irritation, headaches and dizziness, while inhalation of larger concentrations can cause loss of consciousness and eventually death. Long-term health effects may also be possible. Gasoline contains benzene, for example, a known carcinogen with allowable exposure limits of only a few parts per million. Therefore, even working in gasoline vapour atmospheres at levels below 10% LFL requires appropriate industrial hygiene precautions, such as respiratory protection or local exhaust ventilation.
In the past, many gasolines contained tetra-ethyl or tetra methyl alky lead anti-knock additives, which are toxic and present serious lead absorption hazards by skin contact or inhalation. Tanks or vessels which contained leaded gasoline at any time during their use must be vented, thoroughly cleaned, tested with a special “lead-in-air” test device and certified to be lead-free to assure that workers can enter without using self-contained or supplied breathing air equipment, even though oxygen levels are normal and the tanks now contain unleaded gasoline or other products.
Gaseous petroleum fractions and the more highly volatile fuel products have a mild anaesthetic effect, generally in inverse ratio to molecular weight. Lower-boiling-point liquid fuels, such as gasoline and kerosene, produce a severe chemical pneumonitis if inhaled, and should not be siphoned by mouth or accidentally ingested. Gases and vapours may also be present in sufficiently high concentrations to displace oxygen (in the air) below normal breathing levels. Maintaining vapour concentrations below the exposure limits and oxygen levels at normal breathing ranges, is usually accomplished by purging or ventilation.
Cracked distillates contain small amounts of carcinogenic polycyclic aromatic hydrocarbons (PAHs); therefore, exposure should be limited. Dermatitis may also develop from exposure to gasoline, kerosene and distillate fuels, as they have a tendency to defat the skin. Prevention is accomplished by use of personal protective equipment, barrier creams or reduced contact and good hygienic practices, such as washing with warm water and soap instead of cleaning hands with gasoline, kerosene or solvents. Some persons have skin sensitivity to the dyes used to colour gasoline and other distillate products.
Residual fuel oils contain traces of metals and may have entrained hydrogen sulphide, which is extremely toxic. Residual fuels which have high cracked stocks boiling above 370 °C contain carcinogenic PAHs. Repeated exposure to residual fuels without appropriate personal protection, should be avoided, especially when opening tanks and vessels, as hydrogen sulphide gas may be emitted.
Petrochemical feedstocks
Many products derived from crude-oil refining, such as ethylene, propylene and butadiene, are olefinic hydrocarbons derived from refinery cracking processes, and are intended for use in the petrochemical industry as feedstocks for the production of plastics, ammonia, synthetic rubber, glycol and so on.
Petroleum solvents
A variety of pure compounds, including benzene, toluene, xylene, hexane and heptane, whose boiling points and hydrocarbon composition are closely controlled, are produced for use as solvents. Solvents may be classified as aromatic or non-aromatic, depending on their composition. Their use as paint thinners, dry-cleaning fluids, degreasers, industrial and pesticide solvents and so on, is generally determined by their flashpoints, which vary from well below –18 °C to above 60 °C.
The hazards associated with solvents are similar to those of fuels in that the lower flashpoint solvents are flammable and their vapours, when mixed with air in the flammable range, are ignitable. Aromatic solvents will usually have more toxicity than non-aromatic solvents.
Process oils
Process oils include the high boiling range, straight run atmospheric or vacuum distillate streams and those which are produced by catalytic or thermal cracking. These complex mixtures, which contain large paraffinic, naphthenic and aromatic hydrocarbon molecules with more than 15 carbon atoms, are used as feedstocks for cracking or lubricant manufacturing. Process oils have fairly high viscosities, boiling points ranging from 260 °C to 538 °C, and flashpoints above 121 °C.
Process oils are irritating to the skin and contain high concentrations of PAHs as well as sulphur, nitrogen and oxygen compounds. Inhalation of vapours and mists should be avoided, and skin exposure should be controlled by the use of personal protection and good hygienic practices.
Lubricants and greases
Lubricating oil base stocks are produced by special refining processes to meet specific consumer requirements. Lubricating base stocks are light- to medium-coloured, low-volatile, medium- to high-viscous mixtures of paraffinic, naphthenic and aromatic oils, with boiling ranges from 371 °C to 538 °C. Additives, such as demulsifiers, anti-oxidants and viscosity improvers, are blended into the lubricating oil base stocks to provide the characteristics required for motor oils, turbine and hydraulic oils, industrial greases, lubricants, gear oils and cutting oils. The most critical quality for lubricating oil base stock is a high viscosity index, providing for less change in viscosity under varying temperatures. This characteristic may be present in the crude oil feed stock or attained through the use of viscosity index improver additives. Detergents are added to keep in suspension any sludge formed during the use of the oil.
Greases are mixtures of lubricating oils and metallic soaps, with the addition of special-purpose materials such as asbestos, graphite, molybdenum, silicones and talc to provide insulation or lubricity. Cutting and metal-process oils are lubricating oils with special additives such as chlorine, sulphur and fatty-acid additives which react under heat to provide lubrication and protection to the cutting tools. Emulsifiers and bacteria prevention agents are added to water-soluble cutting oils.
Although lubricating oils by themselves are non-irritating and have little toxicity, hazards may be presented by the additives. Users should consult supplier material safety data information to determine the hazards of specific additives, lubricants, cutting oils and greases. The primary lubricant hazard is dermatitis, which can usually be controlled by the use of personal protective equipment together with proper hygienic practices. Occasionally workers may develop a sensitivity to cutting oils or lubricants which will require reassignment to a job where contact cannot occur. There are some concerns about carcinogenic exposure to mists from naphthenic-based cutting and light spindle oils, which can be controlled by substitution, engineering controls or personal protection. The hazards of exposure to grease are similar to those of lubricating oil, with the addition of any hazards presented by the grease materials or additives. Most of these hazards are discussed elsewhere in this Encyclopaedia.
Special products
Wax is used for protecting food products; in coatings; as an ingredient in other products such as cosmetics and shoe polish and for candles.
Sulphur is produced as a result of petroleum refining. It is stored either as a heated, molten liquid in closed tanks or as a solid in containers or outdoors.
Coke is almost pure carbon, with a variety of uses from electrodes to charcoal briquettes, depending on its physical characteristics, which result from the coking process.
Asphalt, which is primarily used for paving roads and roofing materials, should be inert to most chemicals and weather conditions.
Waxes and asphalts are solid at ambient temperatures, and higher temperatures are needed for storage, handling and transportation, with the resulting hazard of burns. Petroleum wax is so highly refined that it usually does not present any hazards. Skin contact with wax can lead to plugging of pores, which can be controlled by proper hygienic practices. Exposure to hydrogen sulphide when asphalt and molten sulphur tanks are opened can be controlled by the use of appropriate engineering controls or respiratory protection. Sulphur is also readily ignitable at elevated temperatures.
Comments are closed.