Fluid catalytic cracking (FCC) is one of the major conversion technologies in the oil refinery industry. FCC currently produces the majority of the world’s gasoline, as well as an important fraction of propylene for the polymer industry. In this critical review, we give an overview of the latest trends in this field of research. These trends include ways to make it possible to process either very heavy or very light crude oil fractions as well as to co-process biomass-based oxygenates with regular crude oil fractions, and convert these more complex feedstocks in an increasing amount of propylene and diesel-range fuels. After providing some general background of the FCC process, including a short history as well as details on the process, reactor design, chemical reactions involved and catalyst material, we will discuss several trends in FCC catalysis research by focusing on ways to improve the zeolite structure stability, propylene selectivity and the overall catalyst accessibility by (a) the addition of rare earth elements and phosphorus, (b) constructing hierarchical pores systems and (c) the introduction of new zeolite structures. In addition, we present an overview of the state-of-the-art micro-spectroscopy methods for characterizing FCC catalysts at the single particle level. These new characterization tools are able to explain the influence of the harsh FCC processing conditions (e.g. steam) and the presence of various metal poisons (e.g. V, Fe and Ni) in the crude oil feedstocks on the 3-D structure and accessibility of FCC catalyst materials.
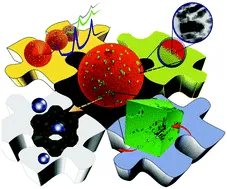
Introduction
Fluid catalytic cracking (FCC) is one of the major conversion technologies in the oil refinery industry and produces the majority of the world’s gasoline. The process is in operation at over 300 out of a total of 646 refineries, as of the beginning of 2014. It is important to note that FCC is not the only conversion process used in oil refineries, as there are also e.g. hydrocracking units. Fig. 1 provides an overview of the different conversion processes in use in oil refineries as of the beginning of 2014, expressed as both the number of barrels of crude oil processed per day and the number of refineries utilizing the processes.1 A number of oil refineries use multiple conversion technologies, and some refineries even have more than one FCC unit. Apart from producing gasoline, the FCC unit is also a major producer of propylene and, to a lesser extent, raw materials for petrochemical processes.
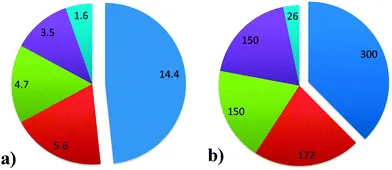
Fig. 1 (a) Installed capacities for the major conversion processes in refineries worldwide, in million barrels per day. (b) Number of refineries in which major conversion processes are installed. Refineries can have more than one technology installed. Data as of 2013, from ref. 1. Color-coding: fluid catalytic cracking (FCC): blue; hydrocracking: red; coking: green; thermal operations: purple; and resid hydrotreating: light blue.
It is estimated that ∼2300 metric tons of FCC catalyst are produced per day,2 or ∼840 000 metric tons per year.
This implies that, on average, approximately 0.16 kg of FCC catalysts are used for the conversion of a barrel of feedstock. This equals about 0.35 lbs per bbl, in units more conventionally used in the field, making use of vacuum gas oil (VGO). Heavier feedstocks, such as resid, require more catalyst material (0.4 lbs per bbl) while lighter feedstocks, such as heavy gas oil (HGO), require less catalyst (∼0.15 lbs per bbl).2 The leading worldwide FCC catalyst producers are W. R. Grace, Albemarle and BASF, while local producers like CCIC in Japan and Sinopec and Petrochina in China have smaller market shares.
In this review article, we will demonstrate that, in spite of the fact that FCC has been practiced for almost 75 years already, the field is still very active and still central in many research activities of both academia and industry. New developments in the availability of feedstocks, such as shale oil and gas and tight oil, the quest to increase the use of renewable resources, as well as changes in the demand for gasoline, result in a desire to change the selectivity of the FCC process. This development has led to a renewed interest in new molecular sieves, zeolites with hierarchical pore structure, and stabilization of the zeolites used in FCC. At the same time a rapid development in analytical tools has recently led to a substantial increase in the fundamental understanding of the integral FCC catalyst particle at sub-micrometer resolution. Reports on new spectroscopic tools used in the analysis of FCC catalyst materials are published in rapid succession. All in all, research in the field of FCC, the grand old lady of zeolite catalysis, is very much alive.