As described earlier, the well-stream may consist of crude oil, gas, condensates, water and various contaminants. The purpose of the separators is to split the flow into desirable fractions.
Test separators and well test
Test separators are used to separate the well flow from one or more wells for analysis and detailed flow measurement. In this way, the behavior of each well under different pressure flow conditions can be defined. This normally takes place when the well is taken into production and later at regular intervals (typically 1-2 months), and will measure the total and component flow rates under different production conditions. Undesirable consequences such as slugging or sand can also be determined. The separated components are analyzed in the laboratory to determine hydrocarbon composition of the gas oil and condensate. Test separators can also be used to produce fuel gas for power generation when the main process is not running. Alternatively, a three phase flow meter can be used to save weight.
Production separators
The main separators shown here are gravity types. On the right, you see the main components around the first stage separator. As mentioned before, the production choke reduces well pressure to the HP manifold and first stage separator to about 3-5 MPa (30-50 times atmospheric pressure). Inlet temperature is often in the range of 100- 150 ºC. On the example platform, the well stream is colder due to subsea wells and risers.
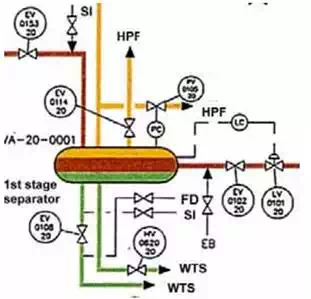
The pressure is often reduced in several stages. In this instance, three stages are used to allow the controlled separation of volatile components. The idea is to achieve maximum liquid recovery and stabilized oil and gas, and to separate water. A large pressure reduction in a single separator will cause flash vaporization, leading to instability and safety hazards.
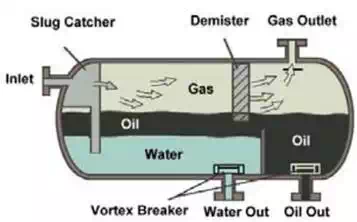
The retention period is typically 5 minutes, allowing gas to bubble out, water to settle at the bottom and oil to be taken out in the middle. In this platform the water cut (percentage water in the well flow) is almost 40%, which is quite high. In the first stage separator, the water content is typically reduced to less than 5%.
At the crude entrance, there is a baffle slug catcher that will reduce the effect of slugs (large gas bubbles or liquid plugs). However, some turbulence is desirable as this will release gas bubbles faster than a laminar flow. At the end, there are barriers up to a certain level to keep back the separated oil and water. The main control loops are the oil level control loop (EV0101 20 above) controlling the oil flow out of the separator on the right, and the gas pressure loop at the top (FV0105 20, above). The loops are operated by the control system. Another important function is to prevent gas blow-by, which happens when a low oil level causes gas to exit via the oil output, causing high pressure downstream. There are generally many more instruments and control devices mounted on the separator. These will be discussed later.
The liquid outlets from the separator will be equipped with vortex breakers to reduce disturbance on the liquid table inside. This is basically a flange trap to break any vortex formation and ensure that only separated liquid is tapped off and not mixed with oil or water drawn in through these vortices. Similarly, the gas outlets are equipped with demisters, essential filters that remove liquid droplets in the gas.
Emergency valves (EVs) are sectioning valves that separate the process components and blow-down valves, allowing excess hydrocarbons to burn off in the flare. These valves are operated if critical operating conditions are detected or on manual command from a dedicated emergency shutdown system. This may involve partial shutdown and shutdown sequences, since the flare may not be able to handle a full blow-down of all process sections simultaneously.
A 45,000-bpd design production with gas and 40% water cut will give about 10 cubic meters from the wellheads per minute. There also needs to be enough capacity to handle normal slugging from wells and risers. This means the separator has to be about 100 cubic meters, e.g., a cylinder 3m in diameter and 14m in length at the rated operating pressure. This means a very heavy piece of equipment, typically around 50 tons for this size, which limits the practical number of stages. Other types of separators, such as vertical separators or cyclones (centrifugal separation), can be used to save weight, space or improve separation.
There must also be a certain minimum pressure difference between each stage to allow satisfactory performance in the pressure and level control loops.
Second stage separator
The second stage separator is quite similar to the first stage HP separator. In addition to output from the first stage, it also receives production from wells connected to the low-pressure manifold. The pressure is now around 1 MPa (10 atmospheres) and temperature below 100ºC. The water content will be reduced to below 2%. An oil heater can be located between the first and second stage separator to reheat the oil/water/gas mixture. This makes it easier to separate out water when initial water cut is high and temperature is low. The heat exchanger is normally a tube/shell type where oil passes though tubes in a heating medium placed inside an outer shell.
Third stage separator
The final separator is a two-phase separator, also called a flash drum. The pressure is now reduced to atmospheric pressure of around 100 kPa, so that the last heavy gas components can boil out. In some processes where the initial temperature is low, it might be necessary to heat the liquid again (in a heat exchanger) before the flash drum to achieve good separation of the heavy components. There are level and pressure control loops.
As an alternative, when production is mainly gas, and remaining liquid droplets have to be separated out, the two-phase separator can be a knockout drum (K.O. drum).
Coalescer
After the third stage separator, the oil can go to a coalescer for final removal of water. In this unit, water content can be reduced to below 0.1%. The coalescer is completely filled with liquid: water at the bottom and oil on top. Internal electrodes form an electric field to break surface bonds between conductive water and isolating oil in an oil-water emulsion. The coalescer field plates are generally steel, sometimes covered with dielectric material to prevent short-circuits. The critical field strength in oil is in the range of 0.2 to 2 kV/cm. Field intensity and frequency as well as the coalescer grid layout are different for different manufacturers and oil types.
Electrostatic desalter
If the separated oil contains unacceptable amounts of salts, they can be removed in an electrostatic desalter (not used in the Njord example). The salts, which may be sodium, calcium or magnesium chlorides, come from the reservoir water and are also dissolved in the oil. The desalters will be placed after the first or second stage separator depending on GOR and water cut.
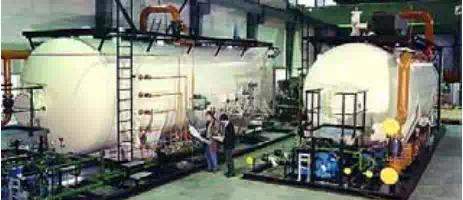