Structure and composition
The FCC process as described above sets a number of demands for catalyst parameters:
• Activity, selectivity and accessibility: first of all, the catalytic properties to convert the large feedstock molecules to the desired molecules;
• Attrition resistance: the catalyst particles must be able to withstand the impacts with each other and the unit walls during circulation;
• Hydrothermal stability: the catalyst must be able to withstand the temperature and steam partial pressure in the regenerator;
• Metals tolerance: the catalyst must be able to withstand the actions of poisons in the (heavier) feedstock;
• Coke selectivity: the catalyst must make the minimum amount of coke at high cracking activity, especially when processing heavier feedstocks, such as resids; and
• Fluidizability: the catalyst components must be available in a form that allows fluidization in the regenerator.
The above demands can be met in a catalyst system that combines a number of components, as depicted in Fig. 7. As described above, the main active component is a zeolite, usually a stabilized form of zeolite Y. This material contains an internal porous structure in which acid sites are present, which can convert larger molecules to the desired gasoline range molecules. Clay is added as filler, but also for heat-capacity reasons. Various alumina and silica sources are used to produce a meso- and macroporous matrix that allows access to, and pre-cracks the larger molecules in the feedstocks. In addition, these components are used to bind the system together. Additional components may comprise specific metal traps for trapping Ni and V. The components are typically mixed in aqueous slurry, and then spray-dried to form more or less uniform spherical particles that can be fluidized in the regenerator.
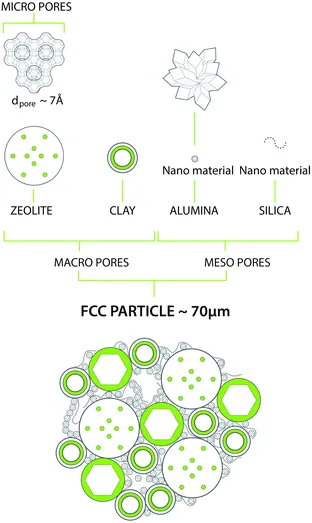
Fig. 7 Typical chemical and structural composition of a FCC particle. Artwork by RSK Communication.
Reactions
Fig. 8, reproduced from the work of Dupain et al., provides a schematic overview of the reactions occurring in the conversion of FCC feedstocks to gasoline range or gas products. It is clear that the conversion occurs in stages, and gasoline is not the primary reaction product, which should be obvious, since the large molecules in the feedstock cannot enter the (∼7.3 Å) pores of zeolite Y. Rather, the large molecules are pre-cracked in the matrix on their way to the zeolites. The cracking reactions are likely a combination between thermal and catalytic reactions, in which the catalytic reaction becomes more important as the molecules get smaller. The catalytic cracking reaction is acid-catalyzed.
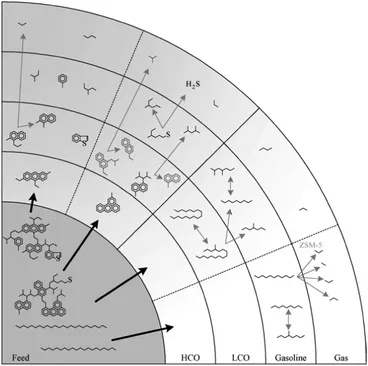
Fig. 8 Consecutive cracking reactions of complex feedstock leading to the final FCC products.
Acidity can be found both at the surface of matrix particles (for instance, Brønsted acidity at silica-alumina interfaces, or Lewis acidity at Al2O3 surfaces), or in the zeolite. The basic structure for zeolites is a tetrahedrally linked silicate. In some lattice positions, the silicon is replaced by aluminum. Since aluminum is present as a trivalent cation, this induces a local negative charge in the lattice, which can be compensated with a proton to form a Brønsted acid site. Lewis acid sites can be formed when the aluminum sites are coordinatively unsaturated when the framework is damaged (e.g. by steaming).
The subject of the cracking mechanism was discussed from the early days of catalytic cracking.33 It is now generally accepted that catalytic cracking involves the formation of carbenium ions.34 As depicted in Fig. 9, there is variety of ways these can be created:
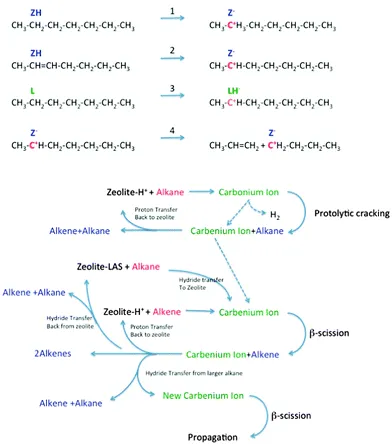
Fig. 9 Reaction network in zeolite-assisted cracking of hydrocarbon molecules. Reaction 1: proton transfer from zeolite Brønsted site to alkane to form carbonium ion. Reaction 2: proton transfer from zeolite to alkene to form carbenium ion. Reaction 3: hydride transfer from alkane to zeolite to form carbenium ion. Reaction 4: Beta scission of a carbenium ion to form a new carbenium ion and an alkene.
(1) Brønsted acid sites can donate a proton to an alkene. This alkene must than have been formed by thermal cracking beforehand. Dupain et al. describe that the initial stages of the FCC process involve mostly thermal (radical) cracking on the outer surface.
(2) Lewis acid sites can abstract a hydride from an alkane, and the same can occur on strong Brønsted sites (forming dihydrogen).
(3) Alternatively, a Brønsted acid site can donate a proton to an alkane, forming a penta-coordinated carbonium ion. When the carbonium ion cracks protolytically (monomolecular, Haag–Dessau), an alkane and a carbenium ion remain.
Isomerization reactions can yield branched molecules, in which the tertiary carbenium ions are more stable. The carbenium ions formed in steps 1–3 crack through β-scission, forming a smaller alkene and a smaller carbenium ion. Hydride abstraction from a larger alkane molecule allows the smaller carbenium ion to desorb from the acid site as an alkane, leaving a new larger carbenium ion on the zeolite acid site to propagate the reaction. Alternatively, the carbenium ion can donate the proton back to the acid site, and desorb as an alkene.
Corma et al. conclude that both pathways, involving initial carbenium ion formation on Lewis sites and initial carbonium ion formation on Brønsted sites, occur in parallel.