Hydrocracking is one of the most versatile refining process for converting heavy fuel oil components into naphtha, kerosene, jet fuel, diesel oil or high-quality lubricating oils, through the catalytic reactions under the high-temperature and high-pressure hydrogen atmosphere.
Types of hydrocracking process
Various types of advanced process technologies are developed and applied to the design of hydrocracking plant.
The flow schemes for the reaction system are categorized into the single-stage reaction system and two-stage reaction system, depending on the types and conversion ratio of feedstock oils and products, and performance of catalyst. In general, the single-stage reactor system is used for producing kerosene and diesel oil economically, and the two-stage reactors system for cracking the feedstock oil completely and increasing the yield of middle distillate oils.
The single-stage reactor system is categorized further into the complete conversion system by recirculating the unconverted oil, and the one-through system that partially convert the oil without recirculation. The configuration will be optimized from the economics and performance.
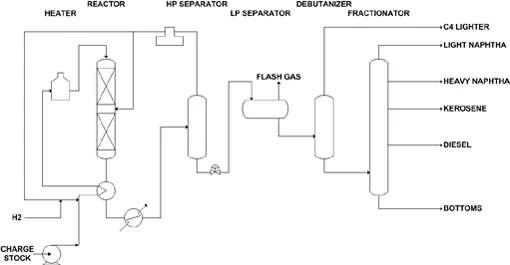
Typical process flow of hydrocracking (single-stage one-through system)
Features and benefits of hydrocracking unit
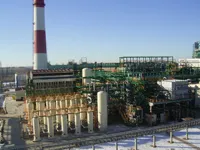
Hydrocracking plant for Yaroslavl Petroleum Refinery
Hydrocracking plant passes the heavy oil onto the catalyst under high-temperature and high-pressure hydrogen conditions, removes impurities through cracking, hydrogenation, isomerization, desulfurization and other chemical reactions, and converts the heavy oil into the valuable light petroleum products. Hydrocracking process is widely used in the recent years especially as a heavy oil upgrading technology that converts heavy oil components into middle distillate for which demands has grown, as one of the major processes along with FCC and thermal cracking.