Catalytic hydrocracking is one of the latest additions to petroleum refining processes, with the first modern commercial unit started up by Chevron in 1958. The interest in hydrocracking has been attributed to the increasing demand for light and middle distillates, the availability of byproduct hydrogen in large quantities from catalytic reforming, and the environmental regulations limiting sulfur and aromatic hydrocarbons in motor fuels [5]. The advantages of hydrocracking include its ability to handle a wide range of feedstocks that may be difficult to process by catalytic cracking and its flexibility in selectivity between light and middle distillates. The principal objective of hydrocracking is to decrease the molecular weight and boiling point of heavy oils to produce saturated hydrocarbons (diesel and jet fuel) from highly aromatic feedstocks (e.g., LCO from FCC) and distillation residua.
The hydrocracking process has two dimensions: Hydrogenation of aromatic rings and cracking of aliphatic compounds, as shown in Figure 7.10, using naphthalene as an example for an aromatic ring system. One should note that that the aromatic rings cannot be cracked before they are saturated with hydrogen. With hydrocracking it is possible to convert an aromatic compound to a paraffinic compounds without any loss of carbon, as shown in Figure 7.10. As a hydrogen-addition process, hydrocracking provides high yields of valuable distillates without producing low-grade byproducts (e.g., heavy oils, gas, or coke) as experienced in carbon rejection processes such as coking.
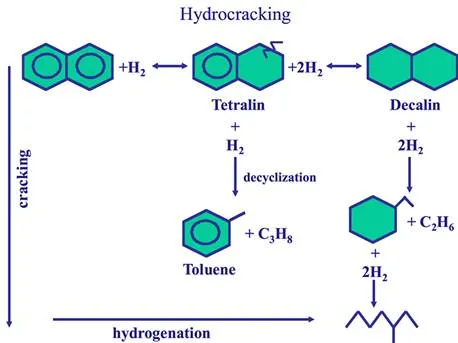
Figure 7.10. Reactions of hydrocracking.
Comments are closed.