The two different reaction systems in hydrocracking, hydrogenation and cracking, are supported by bi-functional catalyst formulations, as illustrated in Figure 7.11. Hydrogenation reactions are promoted by the metal component of the catalysts (e.g., Ni, Co, Mo), and the cracking takes place on catalyst support consisting of silica/alumina. Highly active noble metals (e.g., Pt, and Pd) can be used for hydrogenation of hydrocarbons with extremely low sulfur contents as the noble metals are susceptible to sulfur poisoning.
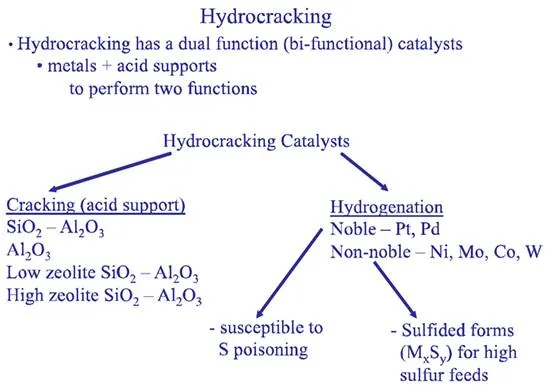
Figure 7.11. Functions of hydrocracking catalysts.
Hydrocracking processes most commonly include two reaction stages: Hydrotreating to remove heteroatom (S, N, O) species and Hydrocracking to increase the H/C ratio of the hydrocarbons in the feeds by hydrogenation and to decrease their molecular weight by cracking. In most cases, the hydrotreating reactor (HT) packed with cobalt-molybdenum catalysts precedes the hydrocracking (HC) reactor typically packed with nickel-tungsten catalysts (for hydrogenation) supported on alumina/silica (for cracking). Figure 7.12 shows different configurations of hydrocracking processes, depending on the heteroatom content of the feeds. For feeds with very low heteroatom contents, hydrocracking without hydrotreating may be applied, but this is very rare. Other process configurations include single stage with dual catalysts, two-stage dual and triple catalysts, as shown in Figure 7.11. The hydrocracking reactions are performed at 300–400°C and 8–15 MPa of hydrogen pressure.